coyotechet
Chet
Chambering runout
I have a very nice South Bend Heavy 10 and for the past few years using my Heavy 10 most of my 6PPC chambers had a runout at the web area of the chamber between .4415 /.4418 which I did not like but was the best I could cut. I tried Floating reamer holders of different types Bald Eagle style pushers and pushing with dead centers. Everything I tried gave me the same results. This past January I decided I was going to find out why I could not cut a smaller chamber. I had already many times checked the lathe bed for both level and twist plus tail stock alignment many times and did the South Bend two bars test chucked up at the headstock and the two bar test between dead centers between at head stock and tailstock. Still always got the .4415 to .4418 or little larger not really very happy.
So the first thing I did was to make me a really nice way to check the tail stock for all types of alignment both for radial and axial plus and most importantly angular. I came up with a two bar and slider ring which really told me a lot about finding the Angular runout which ended up being my trouble with run out. Took me many many hours and days of shimming and even some hand tool scraping to get the tailstock in complete alignment all three ways to under .0005 full travel of the tail stock spindle. The outcome of all this work has really paid off, as I now have cut 5 straight 6 PPC chambers with just using a dead center in the tail stock spindle and getting a runout of .4405 /.4403 best I can check and the last chamber I cut was a 7 LRM with a runout of .5332 (reamer print shows .5530) best I can check Very happy with my outcome.

Adjusting and checking tail stock alignment using my alignment tool. Chuck up the first half of the test bar at the headstock in the chuck and indicate the test bar to .0001 or less. Then chuck up the second half of the test bar in the tail stock and mic the joint of the two halves and then adjust the tail stock until the joint is true to the test bar diameter. Do this with the tail stock spindle all the way in at zero. Now install the slider ring onto the test bar and move it back and forth should not feel the passing of the joint. (Slider ring should be a very close fit to the test bars .0005 or less.) Now crank the tail stock spindle out the full length and check the joint by sliding the slider ring back and forth should not fill the joint if all is true and no angular is in the tail stock.
Chet
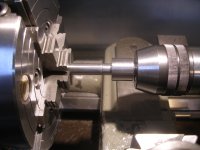
I have a very nice South Bend Heavy 10 and for the past few years using my Heavy 10 most of my 6PPC chambers had a runout at the web area of the chamber between .4415 /.4418 which I did not like but was the best I could cut. I tried Floating reamer holders of different types Bald Eagle style pushers and pushing with dead centers. Everything I tried gave me the same results. This past January I decided I was going to find out why I could not cut a smaller chamber. I had already many times checked the lathe bed for both level and twist plus tail stock alignment many times and did the South Bend two bars test chucked up at the headstock and the two bar test between dead centers between at head stock and tailstock. Still always got the .4415 to .4418 or little larger not really very happy.
So the first thing I did was to make me a really nice way to check the tail stock for all types of alignment both for radial and axial plus and most importantly angular. I came up with a two bar and slider ring which really told me a lot about finding the Angular runout which ended up being my trouble with run out. Took me many many hours and days of shimming and even some hand tool scraping to get the tailstock in complete alignment all three ways to under .0005 full travel of the tail stock spindle. The outcome of all this work has really paid off, as I now have cut 5 straight 6 PPC chambers with just using a dead center in the tail stock spindle and getting a runout of .4405 /.4403 best I can check and the last chamber I cut was a 7 LRM with a runout of .5332 (reamer print shows .5530) best I can check Very happy with my outcome.
Adjusting and checking tail stock alignment using my alignment tool. Chuck up the first half of the test bar at the headstock in the chuck and indicate the test bar to .0001 or less. Then chuck up the second half of the test bar in the tail stock and mic the joint of the two halves and then adjust the tail stock until the joint is true to the test bar diameter. Do this with the tail stock spindle all the way in at zero. Now install the slider ring onto the test bar and move it back and forth should not feel the passing of the joint. (Slider ring should be a very close fit to the test bars .0005 or less.) Now crank the tail stock spindle out the full length and check the joint by sliding the slider ring back and forth should not fill the joint if all is true and no angular is in the tail stock.
Chet
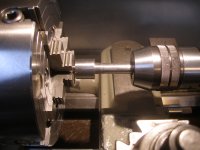
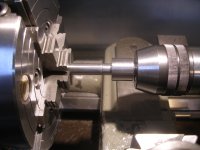