B
bigngreen
Guest
I wanted to update this thread with a big THANKS for the help!! I recently got a new PM 1340 GT lathe, all loaded up with DRO and three phase with VFD and such, I was super excited to give it a run threading. Got the results I was looking for, nice, smooth, sexy threads! I threaded a chunk of Remington factory barrel which has been what's been giving me fits, the brake threads on all the way super smooth and with only four turns on the threads the brake has only .001 play. Super happy and digging the DRO!
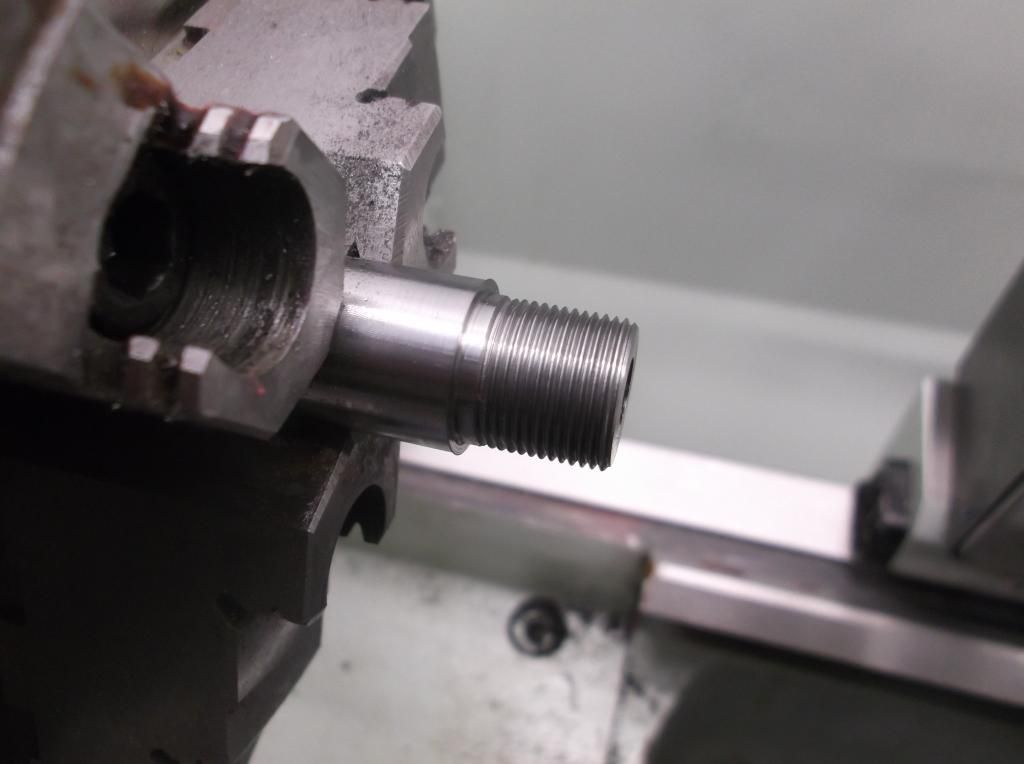
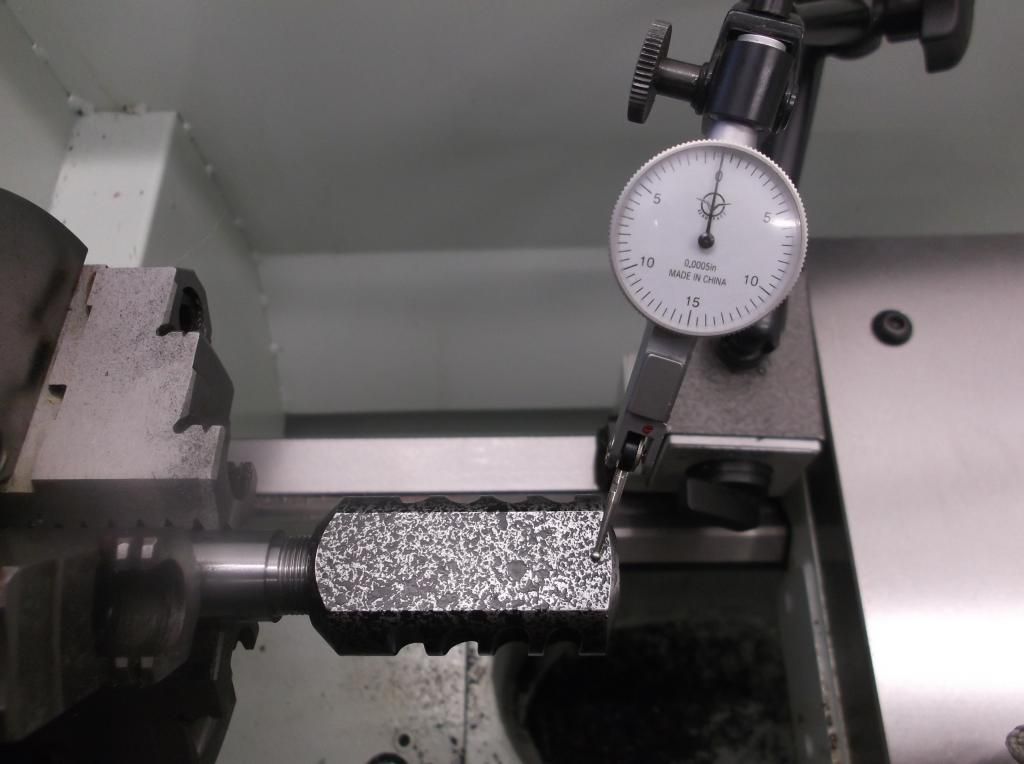
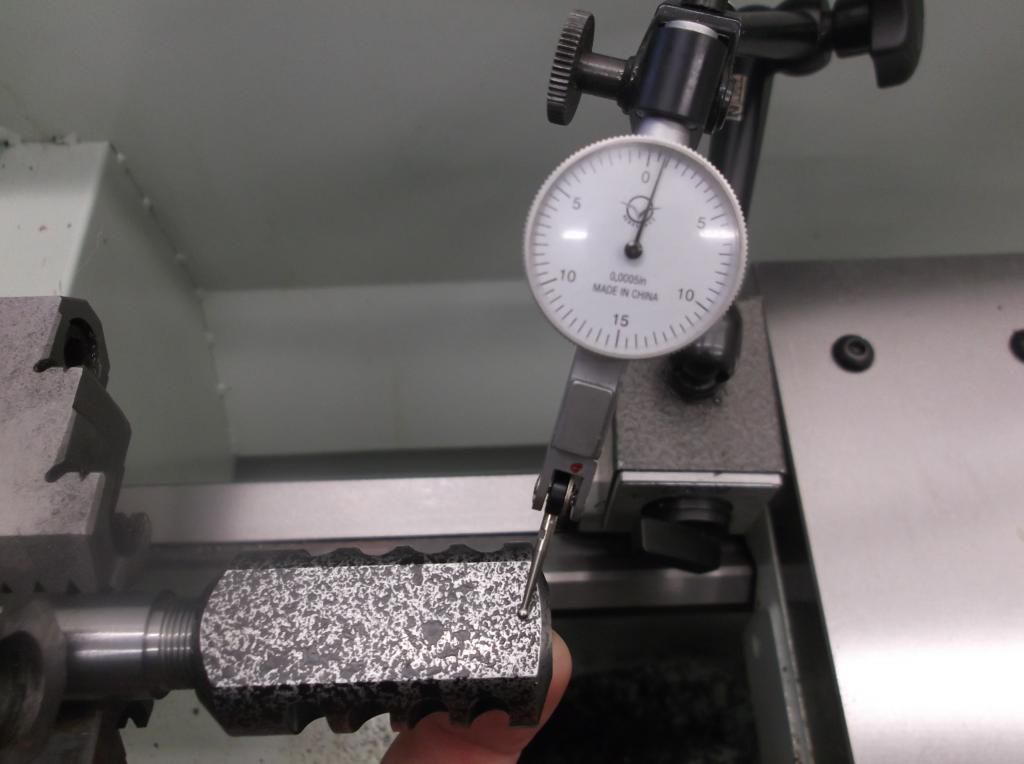