N
NesikaChad
Guest
Lapping pillars with emery around
the action with provide a larger radius , much the same as lapping scope rings
with a 1 inch bar. This can lead to problems in orientation when first
installed. We chamber within tenths, pillars can be machined to a great
fit also...BTW-
I use Norton Blue Bak open coat paper in 600 grit. A sheet of this measures .006" in thickness. I check the fit using a very scientific method that involves sticking the pillar on the receiver and then holding it up to a light source. I don't get much for day light and considering just how small a photon is I feel pretty good about the process.
Considering that my pillars are registered in the stock at a qualified height and clocked square to the relation of bore centerline via the pockets that I machine into the stock I believe I have overcome any alignment concerns. They are about as square as I'm going to get them and investing anymore effort to that is only going to make the minute hand on the clock get further away from getting the job done. To emphasize how accurate this is when setting up in the mill to do the secondary inlets I make it a practice to run an indicator over the top of the receiver and the top showline of the stock. In applications where it's not a bag gun where the barreled action is inclined intentionally, it is very rare for the action and stock not to be very, very parallel to one another.
The rib of pillar material that contacts the bottom of the receiver is .060" wide. This means that .120" of the action's total linear bedding surface length isn't contacting resin. The rib is .05" taller than the contoured base of the pillar which is concentric to the machined inlet I put in the stock.
The amount of resin is concentric for the bulk of a receiver's length. Round, square, dodecahedron shaped; it doesn't matter when the inlet is machined specific to the action being used. I personally feel this is important as it attempts to get a better handle on the whole shrinkage debate which I feel is far more of a concern than .006" of radius difference. Also if the material does yield to tensile pressure applied by the screws at least this way it might be a bit more evenly dispersed. I say that knowing fully well its not that simple as the action is being loaded straight down (I'd be right if it were being inflated against the bedding) so the bulk of the pressure is at the 6 o clock position and then reduces as it gets further away.
Illustrations may help:
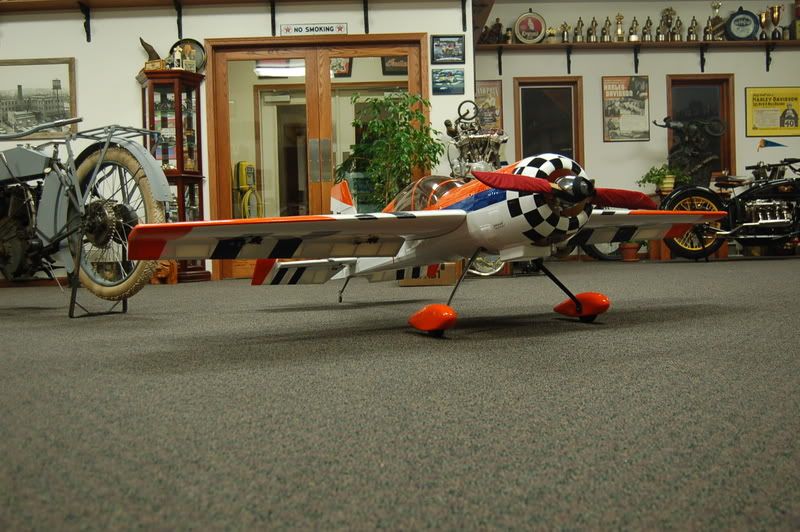
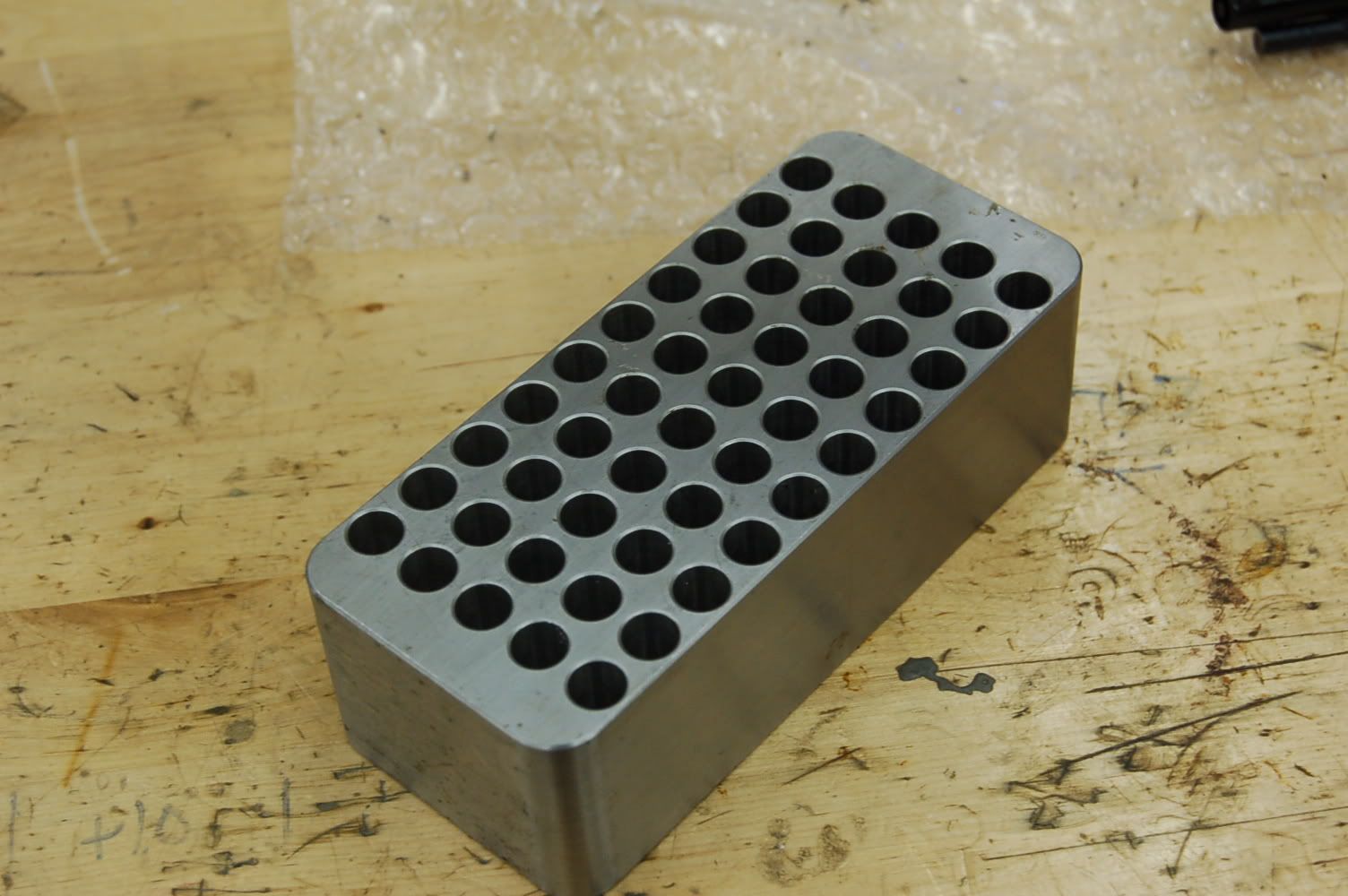
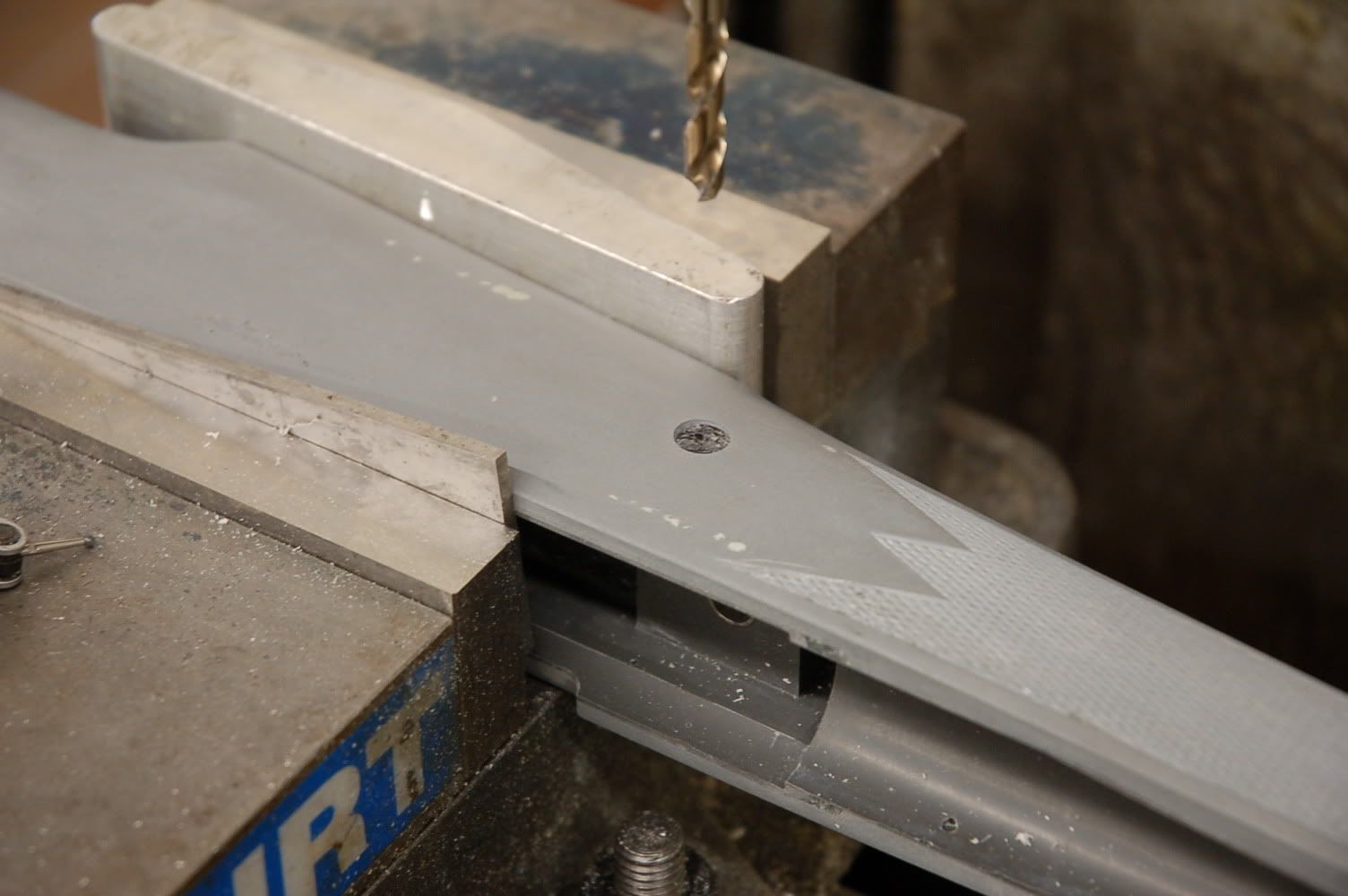
All of this high minded discussion is great and makes for some entertainment, but aren't "true" bench guns glued in anyway? Every Nesika I built on $1000 dollar Terry Leonard carbon/redwood and the myriad of other composite/wood/synthetic bench rest stocks were done this way as it evaporates the whole issue of shrinkage and tolerances. It's not going to move if it's stuck to the stock permanently. So I guess that opens a whole other can of worms. Side by side and spread over the course of a hundred different rifles; is there a clear cut distinction in performance between a glued in gun vs. a bedded one? If that is truly the case then I guess we are all hacks for even having this conversation or continuing to trod down this path. Somehow though I don't think that is the case.
But if it were true. . .
. . .maybe I should just develop a gun where the receiver is molded carbon with a steel slug up front and laid up with the stock all as one piece along with a nitrogen cooled barrel to mitigate thermal distortion due to the OD of the barrel being out of concentricity with the bore C/L I mean all that heat must cause the fat side to swell and elongate which must certainly cause for shots to wander.
Now wouldn't that be something?
Last edited by a moderator: