Here is a little tool some of you might have read me talking about. I will use this tool to check my cone depth when chambering a barrel. I will make another tool just like this one, but a little shorter to check head space with a PT&G go gauge inserted in the chamber. I said i would post a pic when i completed this so here it is. Enjoy and please let me know what you think. remember take it easy i am still learning, And this stuff is way hard for me. LOL!! Lee
I will have a 30 degree cone and a 25 degree cone depending on what action i am chambering for. I thought about making something for Remington type chambers as well? I know these tools are simple to make, but they give me lathe time and i really enjoy making them. Its amazing what you learn each time you turn the machine on. One thing i am already learning, is that i wish i had a heavier machine with more Pony's! Maybe in time. I am actually grateful i have what i have. perfect to learn with. I also just about bet when the time comes i can still make good shooting barrels on this little machine. Anyway enjoy. Lee
One more thing i forgot to mention. You cant see it but under the set screw in the front, on the dial shaft i cut a flat spot with my mill so the set screw has a nice flat spot to set against. This way, with the tight reamed 3/8" hole i dont think the gauge will ever come loose.
Also one thing i ran across while making this tool was that i had to have right around .004 clearance between the cone and the bored shaft so the cone could ride smoothly up and down the bored shaft. I tried to get away with .002 clearance but my machine wouldn't cut smooth enough. Does that make since, or am i not doing something properly? .002 clearance just wouldnt slide. .004 slides real nice, so thats what i had to do. Would HSS tooling make a difference here?
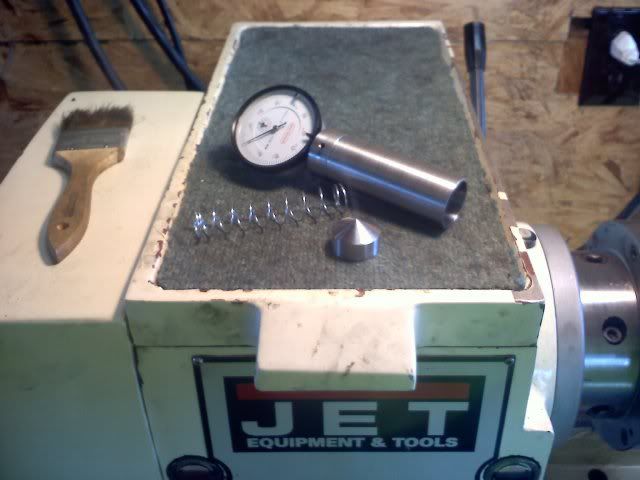
I will have a 30 degree cone and a 25 degree cone depending on what action i am chambering for. I thought about making something for Remington type chambers as well? I know these tools are simple to make, but they give me lathe time and i really enjoy making them. Its amazing what you learn each time you turn the machine on. One thing i am already learning, is that i wish i had a heavier machine with more Pony's! Maybe in time. I am actually grateful i have what i have. perfect to learn with. I also just about bet when the time comes i can still make good shooting barrels on this little machine. Anyway enjoy. Lee
One more thing i forgot to mention. You cant see it but under the set screw in the front, on the dial shaft i cut a flat spot with my mill so the set screw has a nice flat spot to set against. This way, with the tight reamed 3/8" hole i dont think the gauge will ever come loose.
Also one thing i ran across while making this tool was that i had to have right around .004 clearance between the cone and the bored shaft so the cone could ride smoothly up and down the bored shaft. I tried to get away with .002 clearance but my machine wouldn't cut smooth enough. Does that make since, or am i not doing something properly? .002 clearance just wouldnt slide. .004 slides real nice, so thats what i had to do. Would HSS tooling make a difference here?
Last edited: