adamsgt
Jerry Adams
When checking neck thickness as I started to prep new brass I used a fixture from Sinclair that used a dial indicator for measurement.
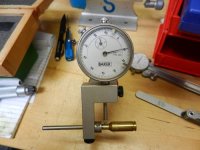
As you can see the neck measured 10 thou. When I finally decided to do a check with a tube mic I got this
: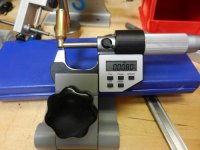
Measured 8 thou with this and a manual tube mic. Also got the same results when I inserted a .008 feeler gauge under the dial indicator tip. Appears that I've been more than little remiss in checking my measuring tools.At this point I wondering if the problem is with the dial indicator itself or how it reads when in the fixture. I'll have to do some more research on that.
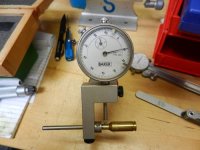
As you can see the neck measured 10 thou. When I finally decided to do a check with a tube mic I got this
:
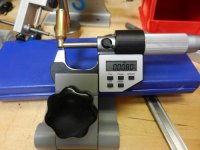
Measured 8 thou with this and a manual tube mic. Also got the same results when I inserted a .008 feeler gauge under the dial indicator tip. Appears that I've been more than little remiss in checking my measuring tools.At this point I wondering if the problem is with the dial indicator itself or how it reads when in the fixture. I'll have to do some more research on that.