Nope - Wrong one. . .
Henrya. . . . No, it's the one on the other end of the picture, that is a 3/8" radius tool. It is kind of hard to see, I will take another picture and attach it.
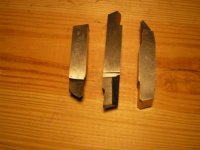
Does this give you a better idea of the tool, all three are set with the cutting edge at the bottom. I have 4-5 of these tools so I set them up in all three directions. On one of the post above they show a cutter with a radius cut in the leading edge of the tool. That is a great tool if you want to take a deep cut and remove a lot of material, but because of the radi it has to move slow, nice chip management, but kind of slow. The nice thing about the cut on the tool I have here is that if you grind it correctly, and that may take some practice, you can turn and face with the same tool, kind of handy if you are facing a part and then going to rough in the OD. It is a good finish tool, but at the stop point you will have a 45 deg. angle to come back and take out with a pointed tool.
There is alot to be said about the insert tooling, if you are doing a lot of the same thing (over and over) that is the tooling, but if you are doing one piece at a time, you can't beat the High Speed tool bit. The investment in the holders (Kits) is kind of pricy, and you could by a box of HS tools for that initial out lay. Really, it comes down to how you feel about the tool you are going to use to do a certain job. If you have a lot of threading to do, by all means get the insert tooling, but if you are doing one at a time over 2 or 3 weeks or longer, does the investment in the tooling justify it? Learning to make a threading tool isn't rocket science, just get a threading guage that is shown it the replys above and learn to make the tool. As I stated above, you only have to be really close, it isn't going to be Quality Controled Inspected an rejected for a 1 or 2 deg. error. I would suggest that you grind a tool - set it up - and put a piece of CRS in the machine and practice with it once to make sure you have it correct. Most of the time you have a receiver or a part that is already threaded and if you do it correctly you will make them interface correctly.
The lathe is best suited to the threading, turning and boring is just getting the feel for holding dimensions. Basically learing that .001 on the dial is either .001 or .002, depending on the graduations on the dial. But, threading will either make or break you, learn to do it right and make the threads look good, if they are tore up or rough you are not doing something right. The leading edge of the threading tool is all that is doing the cutting, the back is just following and if it is draging on the back of the tool it is tearing up material and will ruin the threads, that is the area that is usually going to be where the load is applied, so make it look good. If you have a book on how to set up up for threads, use it. The 30 deg. on the compound is there for a reason, to allow the thread to be controled through the process.
I may have gone overboard on this, but, if you are have a lathe and don't know how to grind your tools - may I suggest that you learn, it is very rewarding to have that ability, then your possibilities are unlimited by your tooling.
Phantom