G'day fellas
Well it's now been 3 months since i sent off my actions to be registered and i'm still waiting for my State firearms registry to get it sorted out....... I've been told that the officer in charge of my applications will be in contact with me next week so hopefully some progress can finialy be made..
So in the mean time i've been keeping my self busy in the workshop building my self a new co-axial bench rest.
I've been attending the 1000 Yd benchrest shoots for the last 12 months and have been drooling over the Farley Coaxial rests a few of the boys have. A few quotes of arround the $1500 mark landed had me thinking i can do better than that..
Well he's the results. About $250 in materials and a few hours of a night over that last 3 weeks..
All CNC'd of course from Aircraft grade aluminium and stainless steel.
Cheers
Leeroy
Well it's now been 3 months since i sent off my actions to be registered and i'm still waiting for my State firearms registry to get it sorted out....... I've been told that the officer in charge of my applications will be in contact with me next week so hopefully some progress can finialy be made..
So in the mean time i've been keeping my self busy in the workshop building my self a new co-axial bench rest.
I've been attending the 1000 Yd benchrest shoots for the last 12 months and have been drooling over the Farley Coaxial rests a few of the boys have. A few quotes of arround the $1500 mark landed had me thinking i can do better than that..
Well he's the results. About $250 in materials and a few hours of a night over that last 3 weeks..
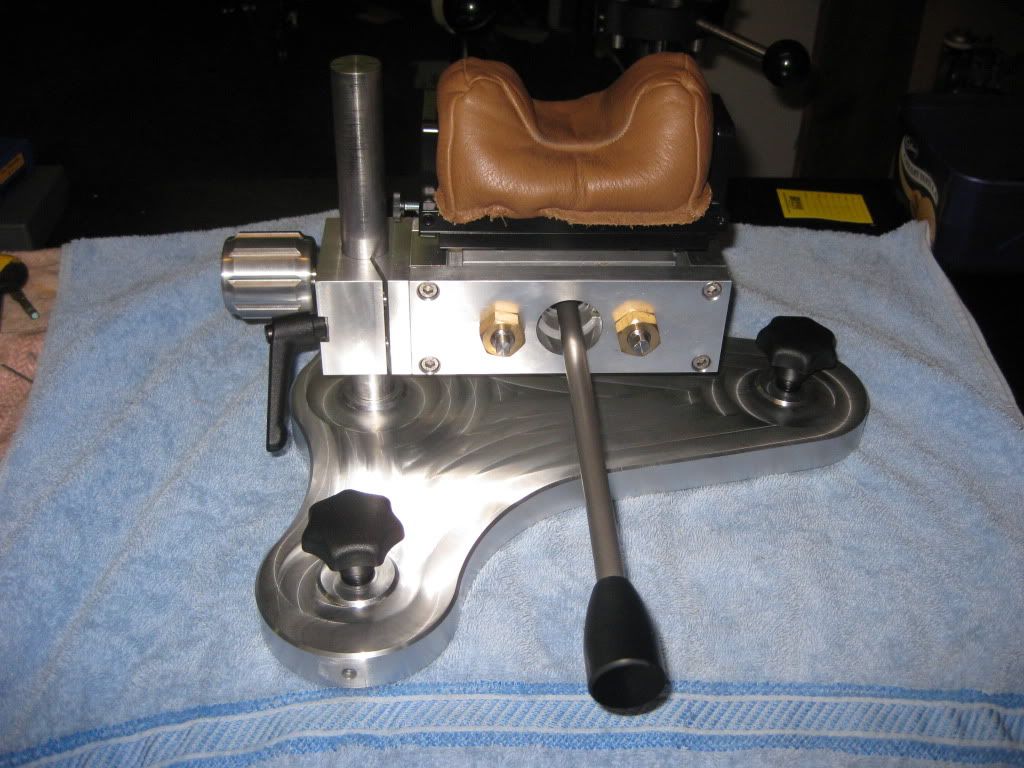
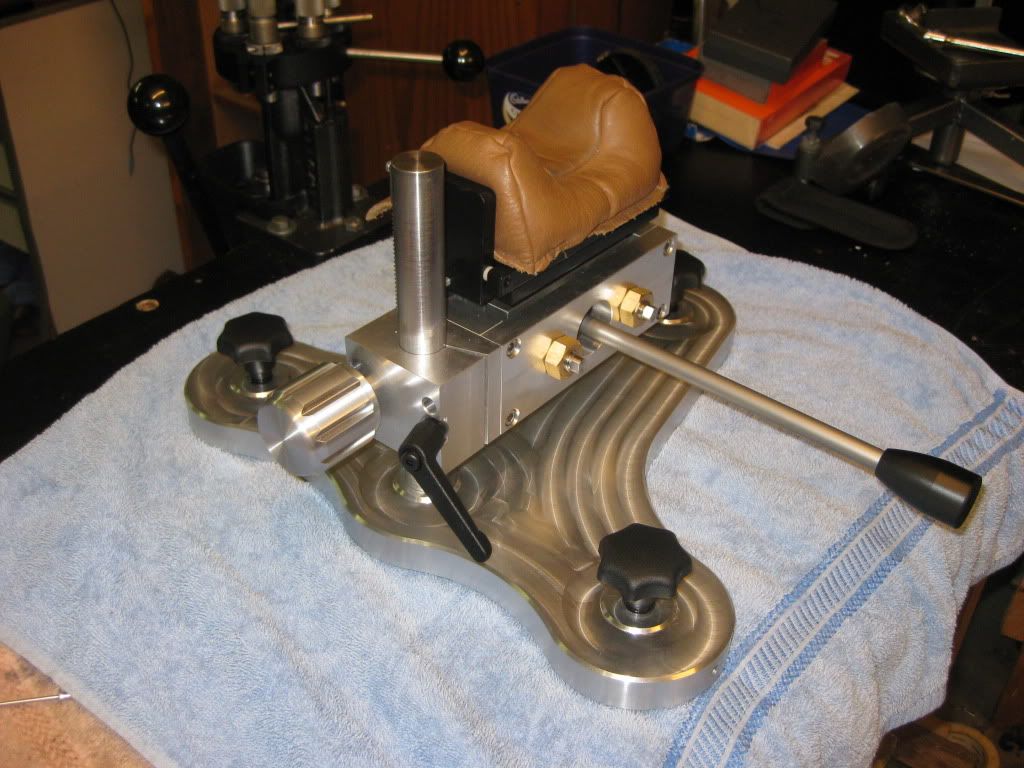
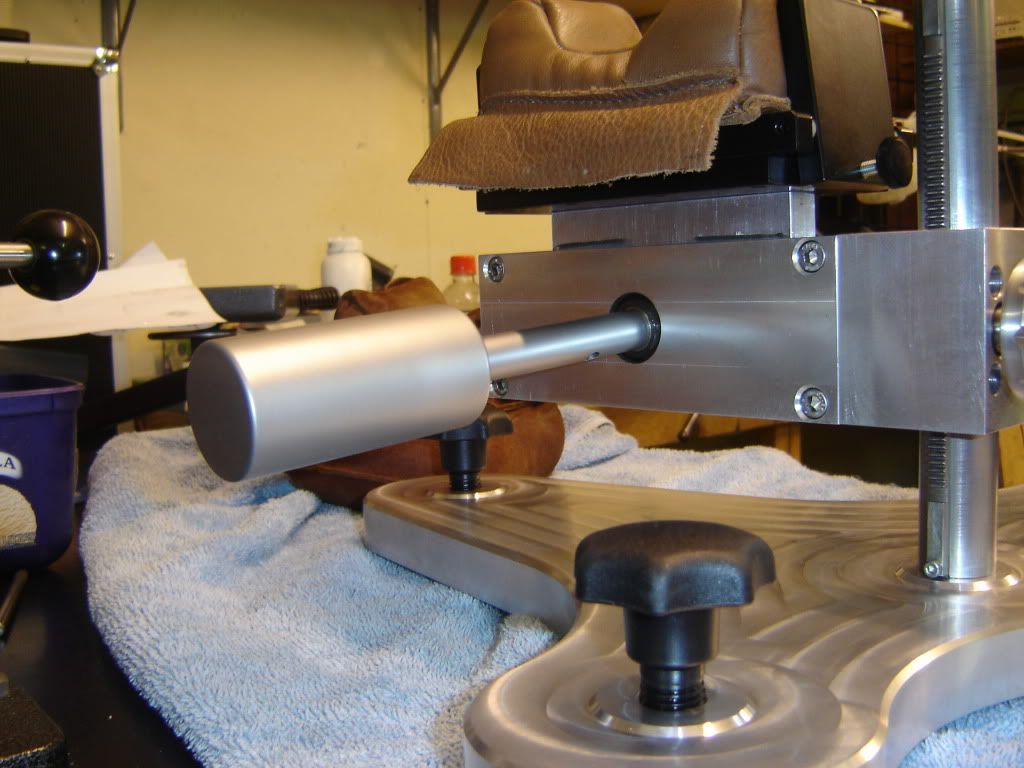
All CNC'd of course from Aircraft grade aluminium and stainless steel.
Cheers
Leeroy
Last edited: