Pointed up 1,000 this morning and decided to add a few more pics. Filled the coffee cup with Island Blend, tossed in Springsteen's 2010 'Darkness on the Edge of Town' double disc set and got to it.....
I like to warm up the point die using a small hair dryer. Every 1,000 jackets, the pivot pins get lubed with a mixture of Permatex clear Ultra Lube and moly paste. A gawd-awful mess, but it works.
The jar holds 1,000 core seated jackets that have been lubed and ready for pointing. A couple hundred are dumped into a new plastic tray and I work out of that. You can see a small rubber cap over the end of the point up punch to protect the end of the punch from getting dinged. Unless I'm actually pointing bullets, it's always on. Don't ask how I learned that lesson.
Probably the most important thing I have is this little notebook. It contains jacket lot numbers, weights, actual jacket length, how much the jackets shorten with different cores/lubes and basically any other pertinent info or observations. For a beginning bullet maker, I can't stress enough how important it is to keep careful notes.
Another 'K' done. The lube is left on until they're ready to be used, then rinsed off with acetone. The acetone flashes off quickly and does a nice job of removing any lube that may get behind the hollow point. The black streaks on the styrene drop tray are from the bullet as it rolls down...one from the back end and one from the front.
I like to warm up the point die using a small hair dryer. Every 1,000 jackets, the pivot pins get lubed with a mixture of Permatex clear Ultra Lube and moly paste. A gawd-awful mess, but it works.
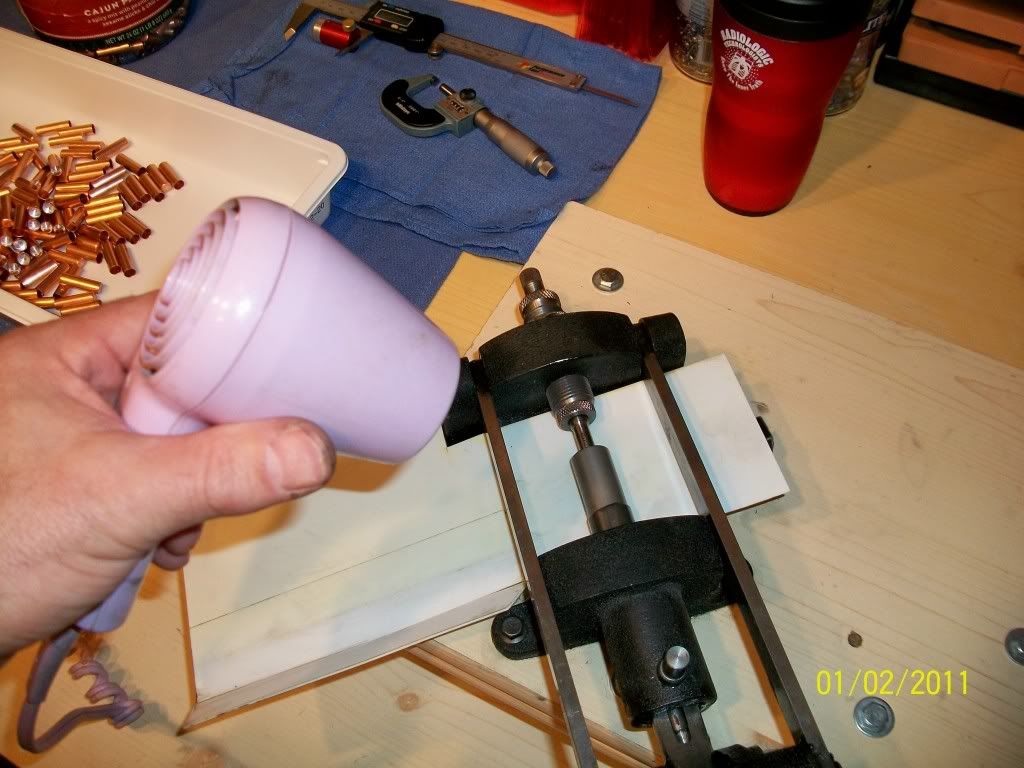
The jar holds 1,000 core seated jackets that have been lubed and ready for pointing. A couple hundred are dumped into a new plastic tray and I work out of that. You can see a small rubber cap over the end of the point up punch to protect the end of the punch from getting dinged. Unless I'm actually pointing bullets, it's always on. Don't ask how I learned that lesson.
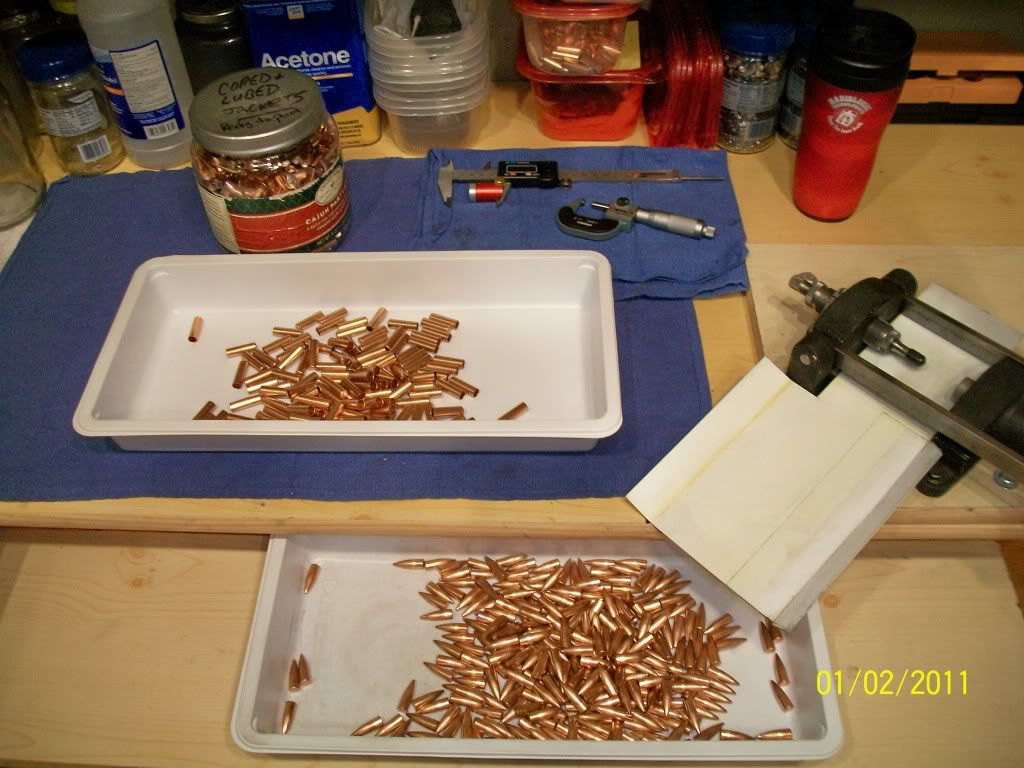
Probably the most important thing I have is this little notebook. It contains jacket lot numbers, weights, actual jacket length, how much the jackets shorten with different cores/lubes and basically any other pertinent info or observations. For a beginning bullet maker, I can't stress enough how important it is to keep careful notes.
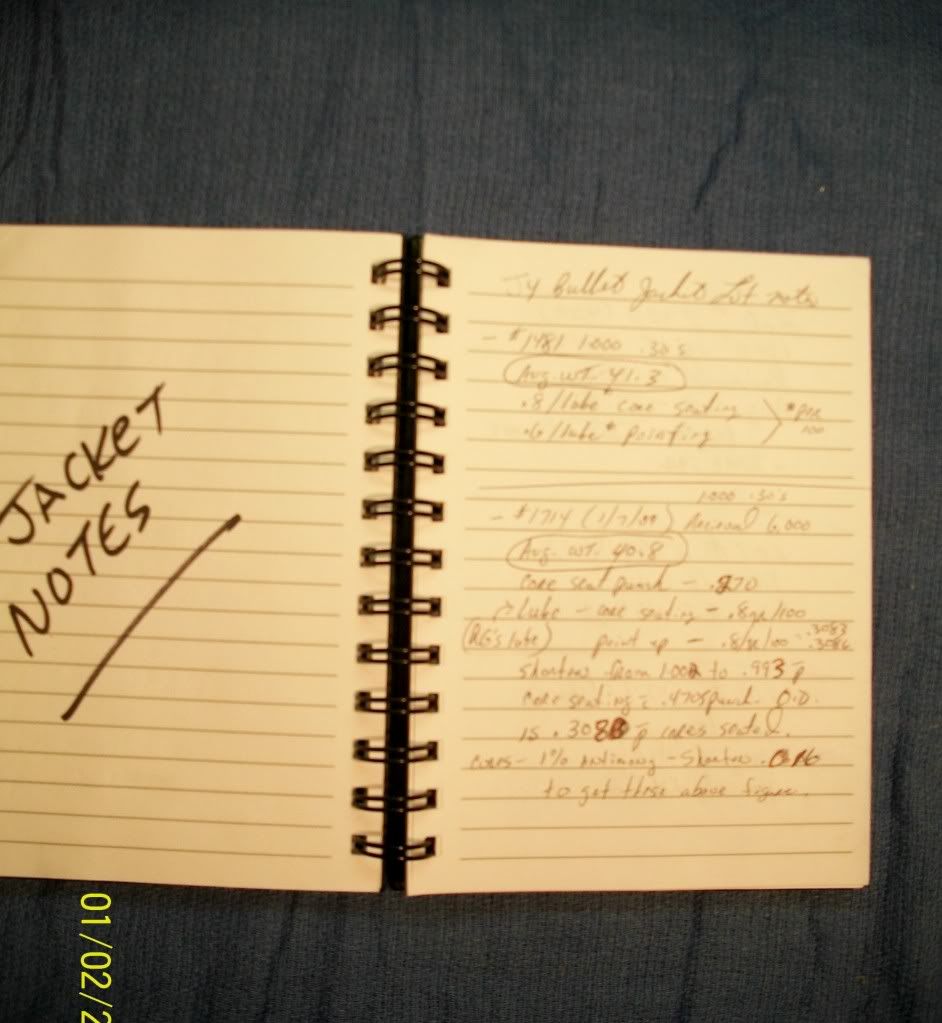
Another 'K' done. The lube is left on until they're ready to be used, then rinsed off with acetone. The acetone flashes off quickly and does a nice job of removing any lube that may get behind the hollow point. The black streaks on the styrene drop tray are from the bullet as it rolls down...one from the back end and one from the front.
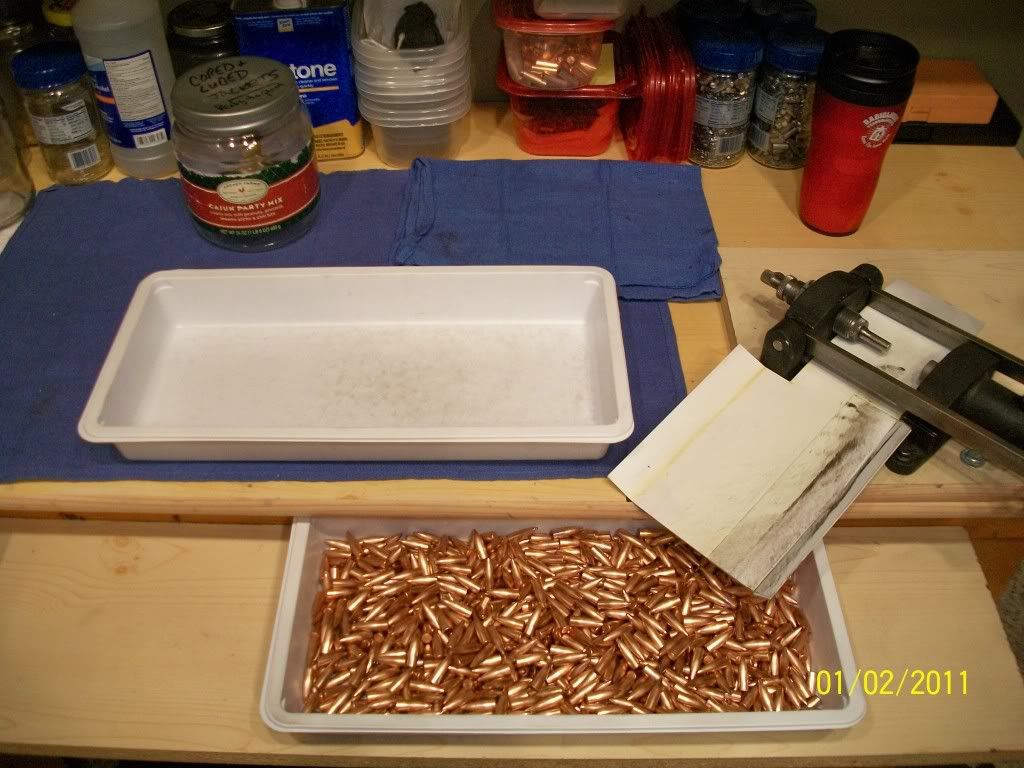
Last edited: