johan teughels
Member
dit my first barrel with a lefthandholder/insert/neg plate upside down (no place enuff on my lathe do do it from the back side ) at 500 rpm (max speed i can start my lathe in S) and it is so easy and clean and quick i wonder why i dit it not before nearly no thread clean up
i got a metric lathe and it is a very slow to thread without unlocking the halfnut and returning in low speed ( i now there is a system i can do it but i am not a real fan of to complicated)
yes i got a recoil lug
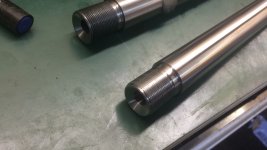
i got a metric lathe and it is a very slow to thread without unlocking the halfnut and returning in low speed ( i now there is a system i can do it but i am not a real fan of to complicated)
yes i got a recoil lug
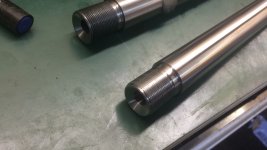